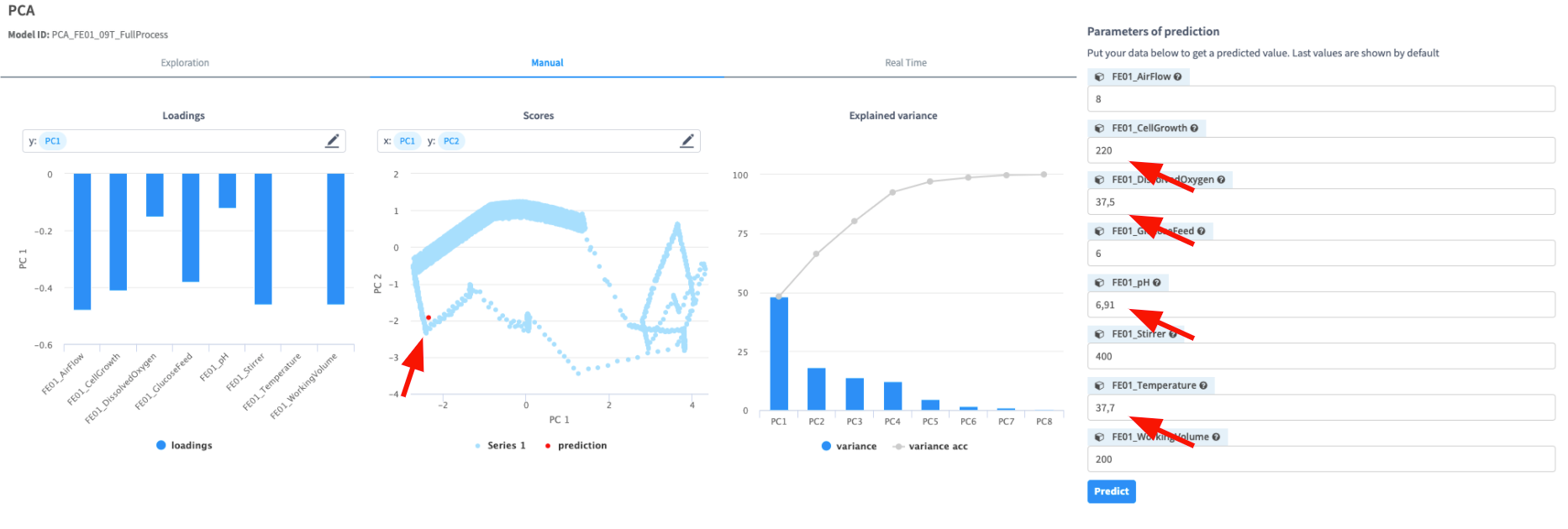
Principal Component Analysis (PCA) is a widely accepted method to use when exploring large, complex data sets to interpret relationships between variables. It transforms complex data tables or data sets to a simpler version with fewer dimensions which contain the same amount of relevant information but makes it easier to visualize the main variations in the data. This makes it more manageable to find similarities and identify why samples are different and which variables contribute to the difference between your samples.
PCA plays an important role in exploratory analysis. It is an unsupervised method which can be used for visualization, data compression for further models, check groups on data (i.e. grouping of different batches), find trends in the data (i.e. trends during a manufacturing process), and detect outliers visually, which may not be easy to identify when checking the variables one at a time, since they are multivariate outliers. It is also used in multivariate process control to combine all available data from a process to a single trace or fingerprint for each operation or group of operations.
Until now, this has been largely a manual effort but technological advances like the Industrial Internet of Things (IIoT), cloud, big data, and artificial intelligence (AI) have opened the door to access computational resources which were not available previously.
Today, Aizon brings the PCA application to market as a ready-to-use component of our GxP AI-enabled cloud platform, specifically designed to provide root cause analysis and predictive deviation capabilities for pharma and biotech manufacturing. The new PCA application uses advanced, multivariate statistics combined with AI to aid pharma and biotech manufacturers to better analyze and control their processes.
Process experts can easily create a scalable PCA model by themselves through a drag-and-drop interface. Furthermore, the PCA tool can be set to work in real-time, ingesting values produced in the moment by the process variables and crunching them into principal component representations; in this way, a process defined by the variation of tens, hundreds or thousands of variables, can be represented in real-time in human-understandable 2D or 3D visual representations of the principal components. Whenever new data is collected, it can be projected into principal components and the new samples plotted in real-time overlapping with previous runs making it possible to identify how similar it is to the current process compared with the previous runs used to create this model.
To learn more about Aizon’s GxP AI-enabled platform and PCA, email us at sales@aizon.com or watch our demo on Multivariate Root Cause Analysis.
Software screen shots:
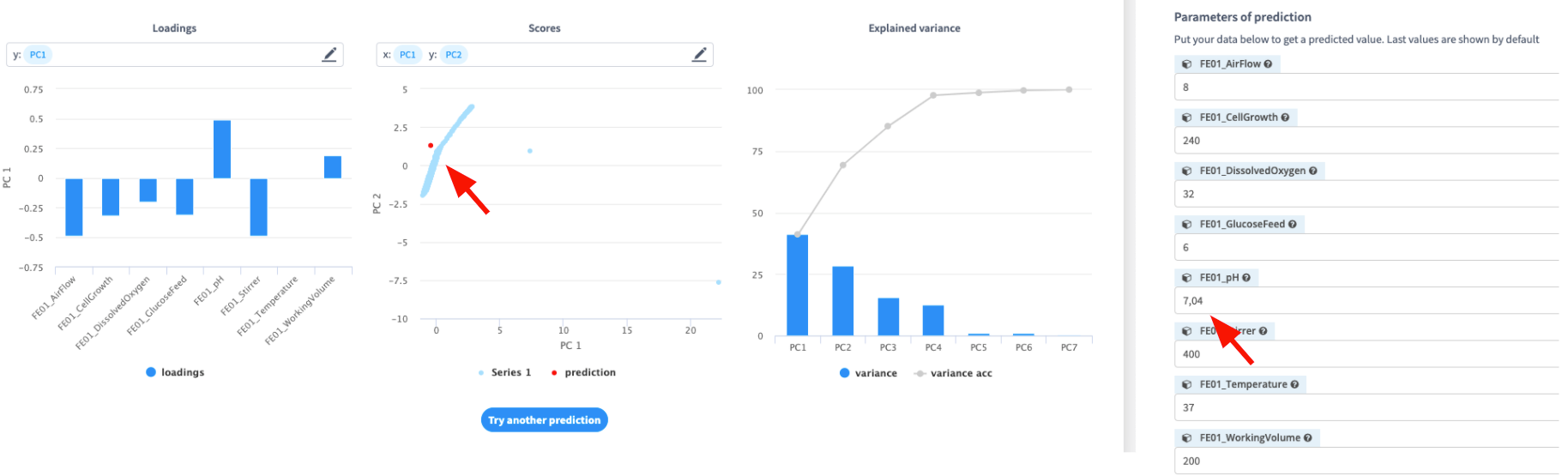
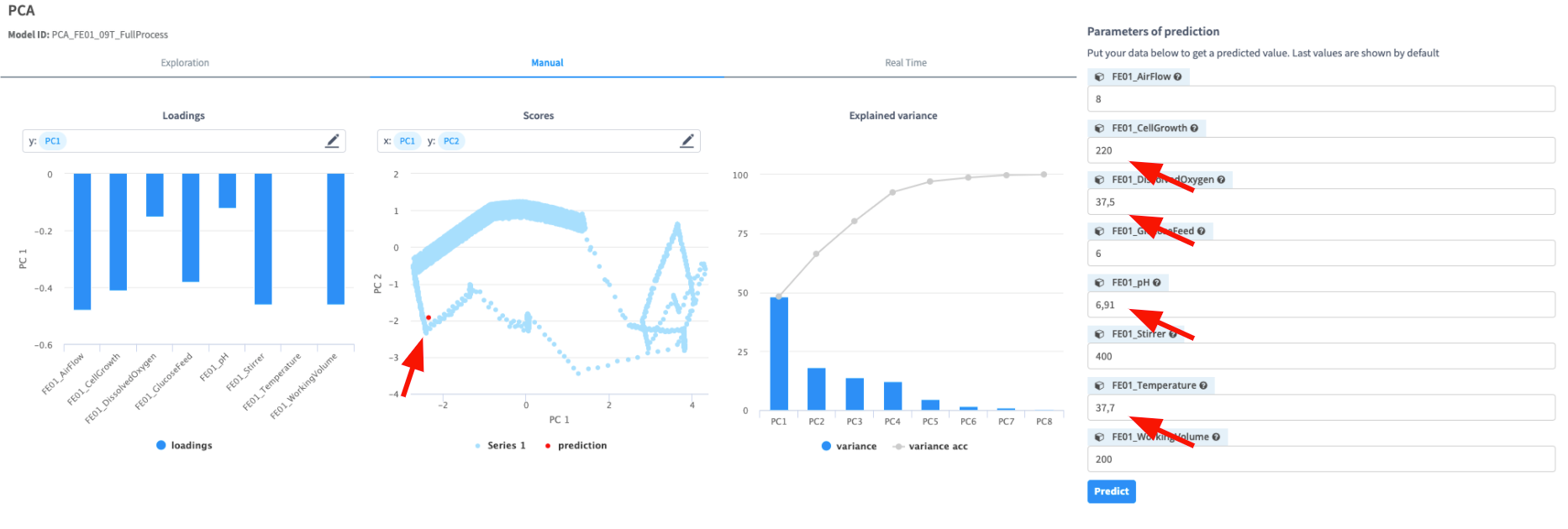