The saying ‘Context is everything’ reminds us that isolated facts, statements, or actions can be deeply misleading without understanding their broader context. It encourages critical thinking and a nuanced approach to interpretation across various domains—including pharmaceutical manufacturing.
Why Data Contextualization Matters in Pharma
In pharmaceutical manufacturing, data is abundant, but without context, it remains just numbers on a screen. Temperature readings, humidity levels, production timestamps—these data points mean little in isolation. Contextualization, however, transforms raw data into meaningful insights by linking it to production processes, batch information, and historical trends. This process is crucial for improving efficiency, ensuring compliance, and enabling predictive analytics.
The Challenges of Disconnected, Siloed Data
As valuable as contextualized data is, for many manufacturers fragmentation stands in the way of achieving it. Pharma companies operate complex manufacturing environments with multiple systems generating data. Equipment such as temperature and humidity sensors collect valuable time-series information, but these records are often stored in disparate systems. A single company may have different setups across its plants—some using modern digital systems, others relying on legacy infrastructure or even paper records. Moreover, IT (Information Technology) and OT (Operational Technology) systems often operate in isolation, further complicating efforts to unify data. Without a comprehensive approach to contextualization, critical data remains siloed, making it difficult to analyze trends, track deviations, or ensure quality control. This fragmentation slows decision-making, increases compliance risks, and limits the ability to fully exploit valuable manufacturing insights.
Taking on the Challenge of Enhancing Data Contextualization
Overcoming these challenges requires more than just ingesting multiple sources of data. The data needs to be contextualized by merging different data sources into a single, powerful analytical framework. Aizon Unify achieves this by combining the best of both a data lake and a data warehouse to create a data lakehouse purpose-built for pharmaceutical manufacturing. This approach ensures that companies can store vast amounts of raw data like a data lake while still enabling fast, structured analysis like a data warehouse.
However, the Aizon platform doesn’t stop there. Its truly unique value lies in the way it goes beyond traditional data lakehouses: it integrates both IT and OT data, providing a comprehensive view of manufacturing processes. IT systems like ERP, MES, and LIMS typically manage structured business and manufacturing execution data, like process orders, yield and delivery windows, while OT systems like PLCs, SCADA, and sensors generate real-time operational data. Aizon Unify blends these two worlds, offering a truly holistic perspective that enhances decision-making. The result is blended contextualization—the culmination of a long-sought goal in manufacturing operations.
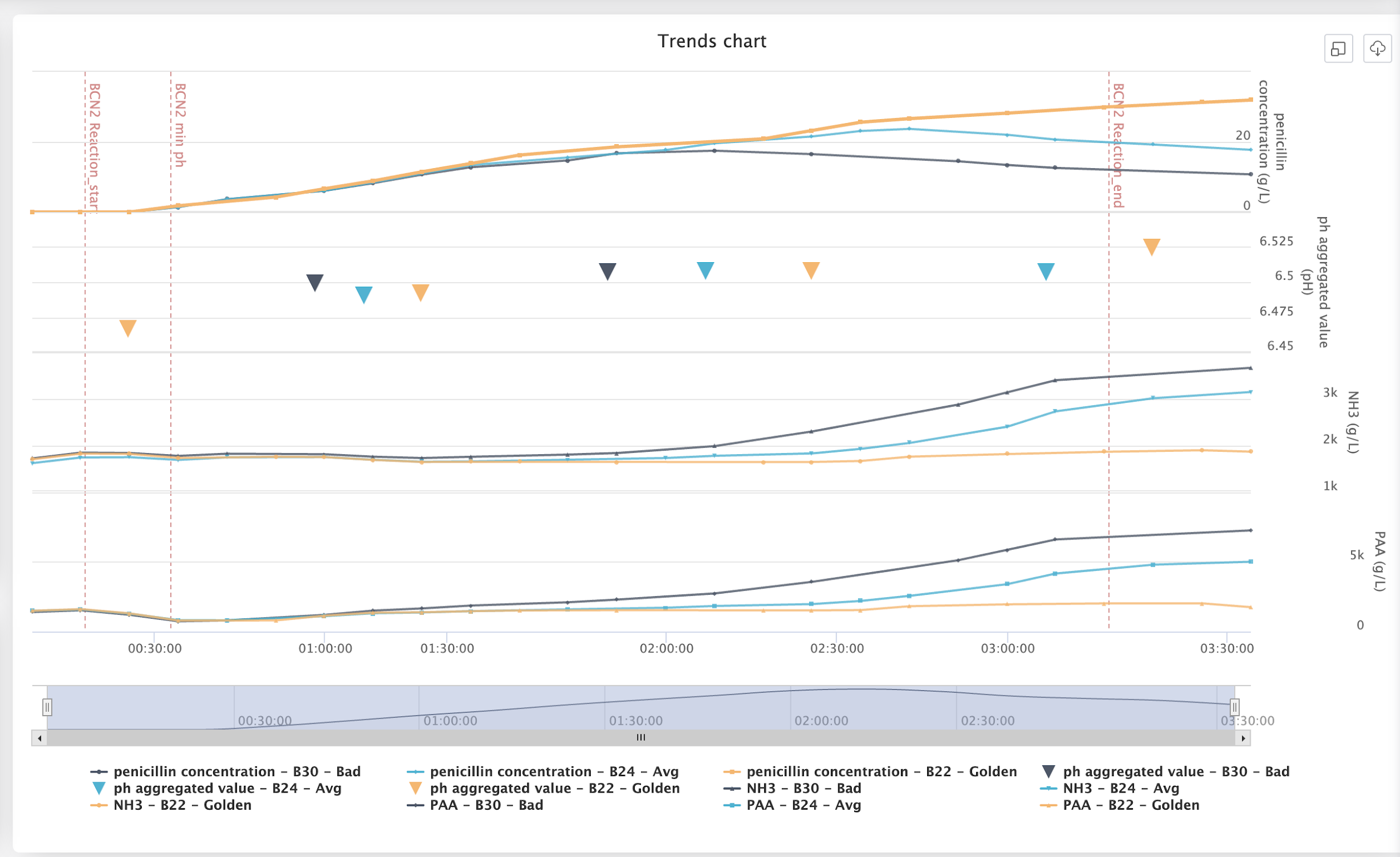
IT and OT Data: Together at Last
Like assembling a jigsaw puzzle, the key to unlocking insights lies in merging disconnected pieces into a coherent whole. Aizon Unify centralizes and contextualizes manufacturing data while enriching it with multiple layers of meaning:
- Source Identification: Through Aizon’s data feeder, each data point is tagged with its origin, including geolocation, plant, production line, and equipment details. The feeder is built with data integrity at its core—a GxP-compliant design that ensures every data point is traceable, attributable, and unaltered. This integrity is what sets Aizon apart from generic data ingestion tools, as in pharmaceutical manufacturing, data must not only be accurate but also trustworthy, audit-ready, and aligned with ALCOA+ principles (Attributable, Legible, Contemporaneous, Original, and Accurate).
- Batch-Level Context: Data is enriched with batch information, linking specific readings to production events. For instance, temperature readings aren’t just numbers—they represent the internal temperature of a medicine during a critical phase of manufacturing.
- Blended Data Insights: By combining IT and OT data, Aizon Unify enables manufacturers to correlate production parameters with real-time machine performance, environmental conditions, and historical records.
- Historical Accessibility: Unlike traditional monitoring systems that store only recent data, Aizon ensures continuous availability of historical records. This means that, as a full-fledged historian, the Aizon platform empowers users to access data from years past as easily as they retrieve recent readings.
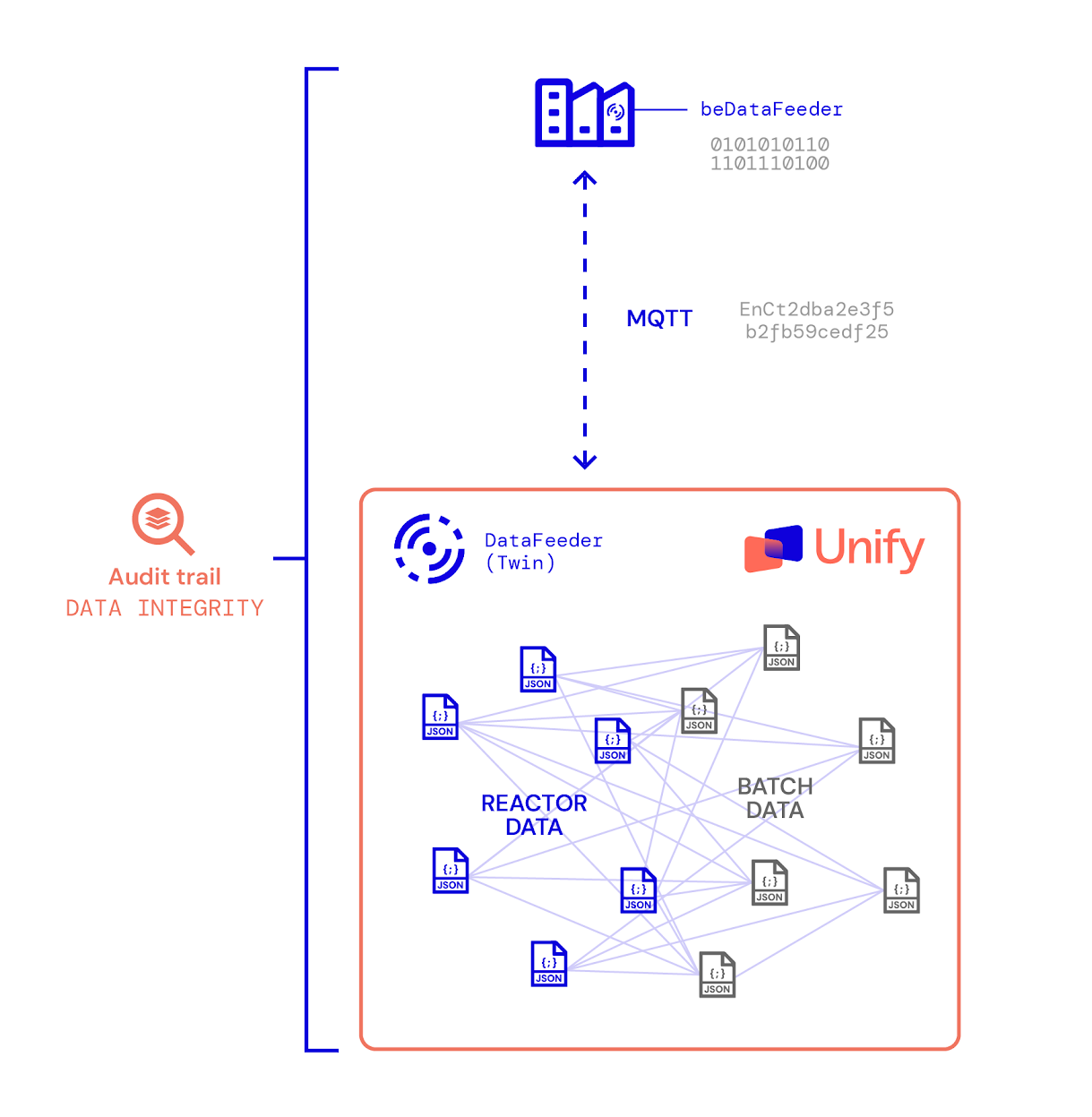
From Contextualized Data to AI-Driven Insights
Once data is fully contextualized and blended, it becomes a powerful analytics asset, unlocking artificial intelligence applications. Data with this level of granularity fuels Aizon Predict to foresee potential deviations and optimize batch performance:
- AI-Enabled Phase Detection: AI can infer when a production phase starts and ends based on historical data, even when this information was previously recorded manually or inconsistently.
- Precision and Compliance Monitoring: Automated tracking eliminates human errors in data entry, such as timestamp inconsistencies due to daylight saving time changes.
- Proactive Deviation Alerts: By analyzing past production cycles, Aizon Predict can detect subtle anomalies and alert manufacturers before deviations escalate into compliance risks.
The Data-Driven Future of Pharma Manufacturing
Ultimately, blended contextualized data lays the foundation for next-generation pharmaceutical manufacturing. By integrating IT and OT data within a unified data lakehouse, breaking down data silos, enhancing efficiency, and unlocking new levels of optimization through AI become a present-day reality.
As the industry keeps moving toward a data-driven future, having the richest and most detailed manufacturing data will be a crucial factor for success. After all, data is the fuel that powers AI, and having the most refined, most powerful kind of fuel is key to ensuring you’re positioned to thrive in the GMP manufacturing landscape of today—and tomorrow.
Watch this Storylane walkthrough for a step-by-step look at how Aizon Unify ingests and contextualizes data: